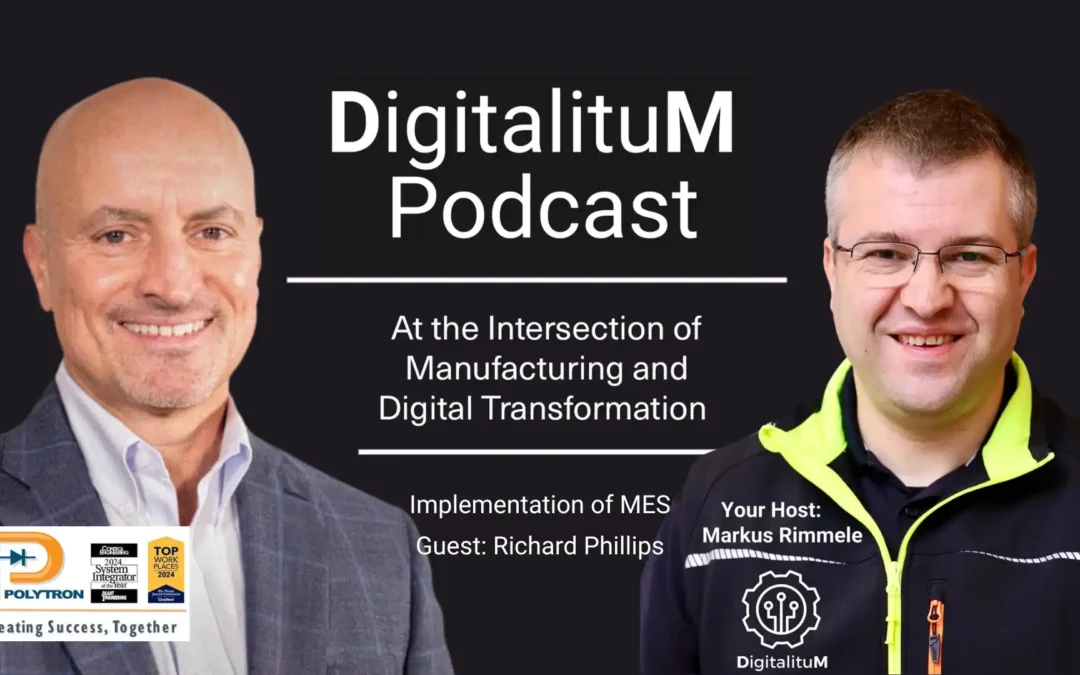
Episode 14 – Unlocking Manufacturing Efficiency
Unlocking Manufacturing Efficiency: The Power of MES with Richard Phillips from Polytron
The DigitalituM Podcast is back with another insightful episode, this time diving into the world of Manufacturing Execution Systems (MES). In this episode, host Markus Rimmele sits down with Richard Phillips, Director of Smart Manufacturing at Polytron, to explore how MES can revolutionize manufacturing operations by improving efficiency, quality, and overall visibility.
If you’ve ever wondered how MES fits into the broader manufacturing technology stack, how it compares to SCADA and ERP, and what manufacturers can do to maximize its impact, this episode is a must-listen.
What is MES and Why Does It Matter?
Manufacturers today operate in an increasingly complex environment. Data silos, inefficiencies, and disconnected systems create barriers to productivity. This is where Manufacturing Execution Systems (MES) come into play.
According to Richard Phillips, MES serves as the critical layer between the shop floor (PLCs, sensors, SCADA) and business systems (ERP, finance, HR). It collects real-time data from machines and processes, providing actionable insights that help manufacturers:
- Improve OEE (Overall Equipment Effectiveness)
- Enhance quality control and traceability
- Optimize production scheduling and inventory management
- Streamline shop floor processes for better decision-making
Without MES, manufacturers often rely on a mix of manual reporting, spreadsheets, and outdated systems, leading to inefficiencies and missed opportunities for improvement.
SCADA vs. MES vs. ERP – Understanding the Differences
One of the biggest misconceptions in manufacturing is the confusion between SCADA, MES, and ERP systems. Many companies use SCADA for monitoring and control, while relying on ERP for business processes, but neglect the critical role of MES in bridging the gap between the two.
Richard explains the ISA-95 model, which structures manufacturing technology into levels:
- SCADA & PLCs → Handle real-time machine control and data collection
- MES → Aggregates and analyzes shop floor data to improve performance and quality
- ERP → Manages business operations, finance, HR, and high-level production planning
Without MES, manufacturers lack the ability to translate raw production data into actionable intelligence. MES is the “handshake” between automation and business systems, ensuring seamless data flow and improved decision-making.
Real-World MES Success Story – Saving $60M with Data
Many manufacturers assume that improving production capacity requires new facilities, more equipment, and significant capital investment. However, MES can unlock hidden efficiencies in existing operations—without spending millions.
Richard shares a compelling case study:
- A small, family-owned manufacturer was preparing to invest $60M in a second plant to expand production.
- After implementing MES, they discovered that their OEE (Overall Equipment Effectiveness) was only 51%, meaning their existing plant was operating at just half of its designed capacity.
- By leveraging MES-driven insights, they optimized production, increasing their OEE to 79% in just six months.
- The result? 55% more production—without needing a new facility.
This case perfectly illustrates how manufacturers can use MES to optimize existing assets before committing to expensive expansions.
Challenges in MES Implementation – Why 80% of Projects Fail
Despite the clear benefits of MES, studies show that 80% of MES pilot projects fail to scale beyond the initial phase. Why?
Richard identifies two main reasons:
1. Lack of Business Alignment – Companies often approach MES as a technology project rather than a business improvement initiative. MES projects struggle to gain traction without clear business drivers and alignment with stakeholders.
2. Poor Change Management – People, processes, and technology must be in sync. If operators resist new technology or processes remain outdated, MES adoption stalls. Richard shares an example where operators resisted MES because it revealed lower OEE numbers, impacting their bonuses. Companies must align incentives and communicate the value of MES to employees.
The solution? Following best practices, selecting scalable MES platforms, and ensuring alignment across teams before implementation.
The Future of MES – AI, Cloud, and Agile Manufacturing
MES is evolving beyond traditional applications, with AI, cloud adoption, and intuitive interfaces shaping the future.
- AI-Powered Insights – Future MES solutions will automatically analyze historical data, predict failures, and automatically recommend process optimizations.
- Cloud-Based MES – Moving MES to the cloud enables scalability, real-time collaboration, and cost savings, making it more accessible for small and mid-sized manufacturers.
- User-Friendly Interfaces – MES platforms are shifting towards intuitive, smartphone-like applications, making adoption easier for shop-floor workers.
Manufacturers must choose MES partners to adapt to these changes, ensuring they stay competitive in the Industry 4.0 era.
Listen to the Full Episode & Learn More
Ready to explore how MES can transform your manufacturing operations? Listen to the full episode with Richard Phillips on the DigitalituM Podcast for expert insights, case studies, and practical implementation tips.
- View Now on youTube: DigitalituM Podcast
- Learn more about Polytron: www.polytron.com
- Connect with Richard Phillips: LinkedIn